In addition to being used as high-temperature, wear-resistant, and corrosion-resistant materials in traditional industries such as machinery, chemical, and metallurgy, engineering ceramics are also being increasingly applied in strategic emerging industries such as aerospace, electronic information, new energy, and energy conservation and environmental protection.
1. Application of Ceramic Materials in Aerospace
Materials used in the aerospace field are mostly utilized in extreme environments such as ultra-high temperature, high vacuum, and strong radiation. These materials require characteristics such as high specific strength, high specific modulus, high temperature resistance, and ablation resistance. Although the market size of the aerospace field is limited, the high-performance requirements for materials have significantly promoted the development and technological advancement of engineering ceramics.
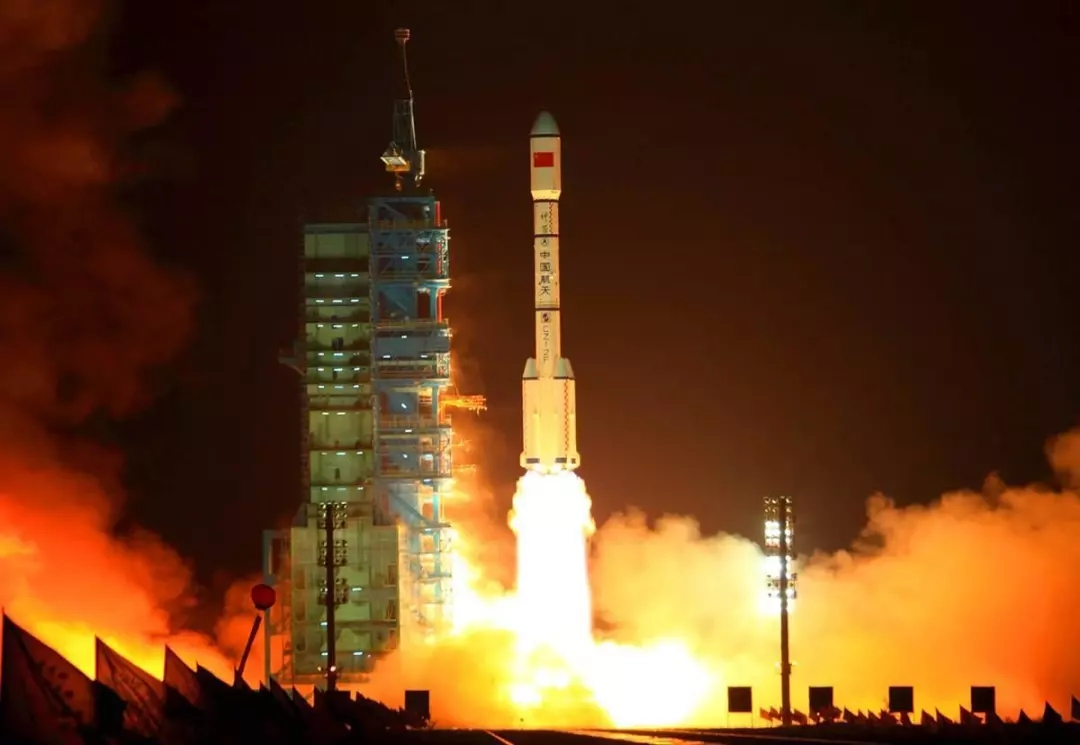
- Ceramic matrix composites for spacecraft shells. Ceramic fiber-reinforced ceramic matrix composites, such as carbon fiber or silicon carbide, have become indispensable materials for manufacturing spacecraft shells and rocket nozzles (thrust chambers).
- Ultra-high temperature ceramic coatings like HfB2, ZrB2, and ZrC . With the development of hypersonic vehicles, the requirements for surface ablation resistance and atmospheric erosion resistance have increased. Ultra-high temperature ceramics such as HfB2, ZrB2, and ZrC are irreplaceable as high-temperature coating materials to enhance the ablation and erosion resistance of vehicle surfaces.
- Nitride composites for high-temperature wave-transparent materials. Nitride ceramics such as silicon nitride and boron nitride have excellent properties like high temperature resistance, low dielectric constant and loss, creep resistance, and oxidation resistance. They can be used as next-generation wave-transparent materials but are challenging to use under the harsh conditions of hypersonic vehicle radomes. Therefore, nitride composites will be the development direction for high-temperature wave-transparent materials. Hexagonal boron nitride ceramics have good thermal conductivity and microwave penetration, making them suitable for radar window materials. Additionally, their low density makes them suitable for high-temperature structural materials in aircraft.
2. Application of Ceramic Materials in the Electronic Information Field
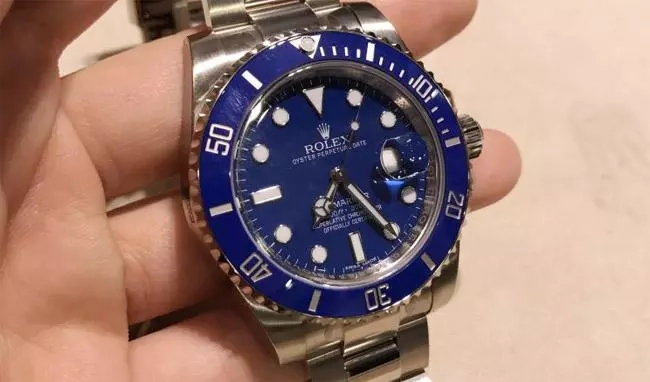
- Ceramic circuit substrates. Engineering ceramics play a crucial role in technological advancements in the electronic information field. Aluminum nitride, alumina, and sapphire substrates are increasingly used in highly integrated circuit boards.
- Wide-bandgap semiconductor materials. The development of wide-bandgap semiconductor materials such as silicon carbide can significantly improve the performance of existing silicon integrated circuits, which is crucial for the development of high-power and high-density integrated circuit chips.
- Ceramics in optical fiber and connectors. Optical fibers and connectors for network information transmission are made from high-purity quartz glass fibers and zirconia ceramics, respectively.
- Laser-emitting crystals. The laser-emitting crystals in solid-state lasers are mainly ruby or yttrium aluminum garnet.
- Piezoelectric ceramics in cameras. The autofocus system of cameras relies on piezoelectric ceramics.
- Ceramic materials for electronic product casings. The casings of smartphones and watches are increasingly using zirconia ceramics, which have a smooth surface and good wear resistance.
3. Application of Ceramic Materials in the New Energy Field
- Anode and cathode materials for lithium batteries. Engineering ceramics have a broad range of applications in the new energy field. Familiar lithium-ion battery cathode materials include LiCoO2, LiMnO2, Li(Co, Ni, Mn)O2, and LiFePO4, which are all ceramic materials. Carbon materials used as anodes are also being increasingly replaced by ceramics.
- Zirconia ceramics as membrane materials for high-temperature fuel cells.
- Silicon carbide ceramics for the light absorption and heat conduction materials in concentrated solar power plants.
- Boron-containing ceramics such as boron carbide as neutron absorbers in nuclear reactors for power generation.
- Carbide coatings and composite coatings of nitrides and carbides can be used as tritium-resistant coatings in nuclear fusion reactors.
- Silicon nitride ceramic bearings for wind power generation, which are highly reliable and maintenance-free.
- Boron nitride crystals, when doped, can emit ultraviolet light and can be used to make ultraviolet semiconductor lasers. Silicon-based boron nitride thin films, which have photoelectric effects, can be used to make photovoltaic cells.
With further development in new energy technology, the application of engineering ceramics in this field will also expand.
4. Application of Ceramic Materials in the Field of Energy Conservation and Environmental Protection
Engineering ceramics have very broad applications in the field of energy conservation and environmental protection, which is also a key direction for the development of the engineering ceramics industry.
- High-porosity ceramic materials for thermal insulation. Lightweight thermal insulation materials with high closed porosity, such as alumina hollow spheres and foam ceramic products, and high-temperature resistant materials like alumina fibers or mullite polycrystalline wool can be used as thermal insulation materials at temperatures ranging from 1000 to 1700℃, effectively saving energy. Additionally, ceramic materials generally have a high emissivity, promoting radiant heat transfer when used as lining materials for industrial furnaces, resulting in faster heating rates and uniform furnace temperatures. Titanium nitride films have low emissivity and high transmittance in the visible light region and some reflectivity in the near-infrared region, making them efficient energy-saving films.
- High-porosity ceramic membranes for gas separation and wastewater treatment. Ceramic membranes with high open porosity can achieve gas-solid separation of high-temperature flue gas and industrial dust-containing gases, effectively removing particles as small as 2.5 microns and smaller dust. They also have good backflush regeneration effects. Ceramic membranes can withstand temperatures above 1400℃ and resist erosion by various acids, alkalis, and corrosive gases, offering long service life. In industrial wastewater and municipal drinking water treatment, ceramic membranes are gradually replacing polymer membranes due to their superior corrosion resistance, regenerability, and longer service life, gaining wider applications.