Black fused alumina, also known as black aluminum oxide, is a type of abrasive material that has been gaining attention for its unique properties and applications in the coated abrasives industry. This blog delves into the various aspects of black fused alumina and its potential uses in coated abrasives.
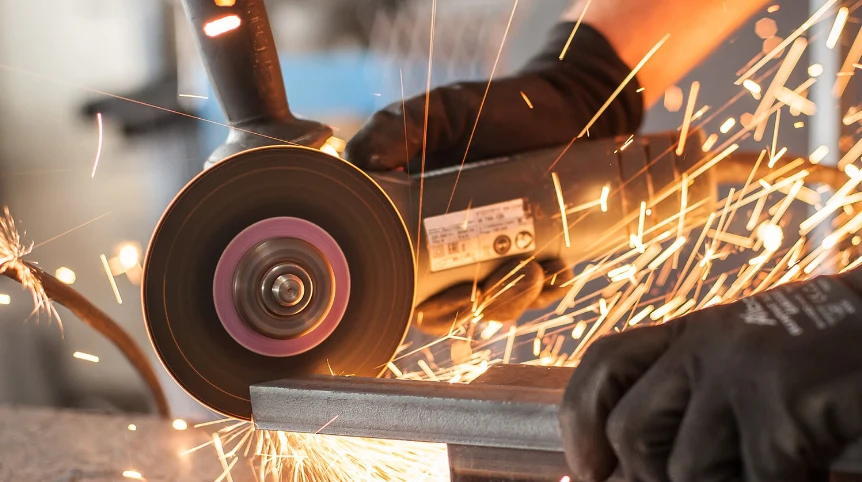
Understanding Black Fused Alumina
Black fused alumina is produced by fusing bauxite and iron filings in an electric arc furnace at high temperatures. The resulting product is a hard, tough abrasive with a sharp-edged grain structure. Its distinctive black color is due to the presence of iron and other impurities.
Properties of Black Fused Alumina
- Hardness: Black fused alumina is characterized by its high hardness, which makes it suitable for aggressive grinding and cutting applications.
- Toughness: The toughness of black fused alumina allows it to withstand high-pressure applications without breaking down easily.
- Heat Resistance: It can endure high temperatures without losing its abrasive properties, making it ideal for high-speed grinding.
- Sharp Edges: The sharp-edged grains of black fused alumina provide efficient cutting action, leading to better material removal rates.
- Cost-Effectiveness: Compared to other abrasive materials like white aluminum oxide or silicon carbide, black fused alumina is more cost-effective while offering comparable performance.
Applications in Coated Abrasives
Coated abrasives, such as sandpaper, abrasive belts, and abrasive discs, are widely used in various industries for finishing, polishing, and material removal. Black fused alumina plays a significant role in enhancing the performance of these coated abrasives.
- Abrasive Belts: Black fused alumina abrasive belts are used for grinding and polishing metals, wood, and composite materials. Their high hardness and toughness ensure long-lasting performance even under intense use.
- Sandpaper: Sandpaper made with black fused alumina is ideal for surface preparation, smoothing rough surfaces, and removing paint or rust. The sharp grains provide a consistent scratch pattern and efficient material removal.
- Abrasive Discs: Abrasive discs with black fused alumina are commonly used in angle grinders and orbital sanders for various applications, including deburring, blending, and finishing.
- Specialty Coated Abrasives: Black fused alumina is also used in specialty coated abrasives designed for specific applications, such as sharpening tools, shaping edges, and fine finishing.
Advantages of Using Black Fused Alumina in Coated Abrasives
- Improved Durability: The toughness and heat resistance of black fused alumina contribute to the longevity of coated abrasives, reducing the frequency of replacement and lowering operational costs.
- Enhanced Performance: The sharp-edged grains ensure efficient cutting action, leading to faster material removal and improved surface finishes.
- Versatility: Black fused alumina can be used on a wide range of materials, including metals, wood, plastics, and composites, making it a versatile choice for various industries.
- Cost Efficiency: As a more affordable abrasive material, black fused alumina offers excellent value for money without compromising on performance.
Conclusion
The exploration of black fused alumina in the coated abrasives field reveals its potential to enhance the performance and cost-effectiveness of various abrasive products. Its unique properties, such as high hardness, toughness, and sharp-edged grains, make it an ideal choice for a wide range of applications. As industries continue to seek efficient and durable abrasive solutions, black fused alumina stands out as a promising material that meets these demands.