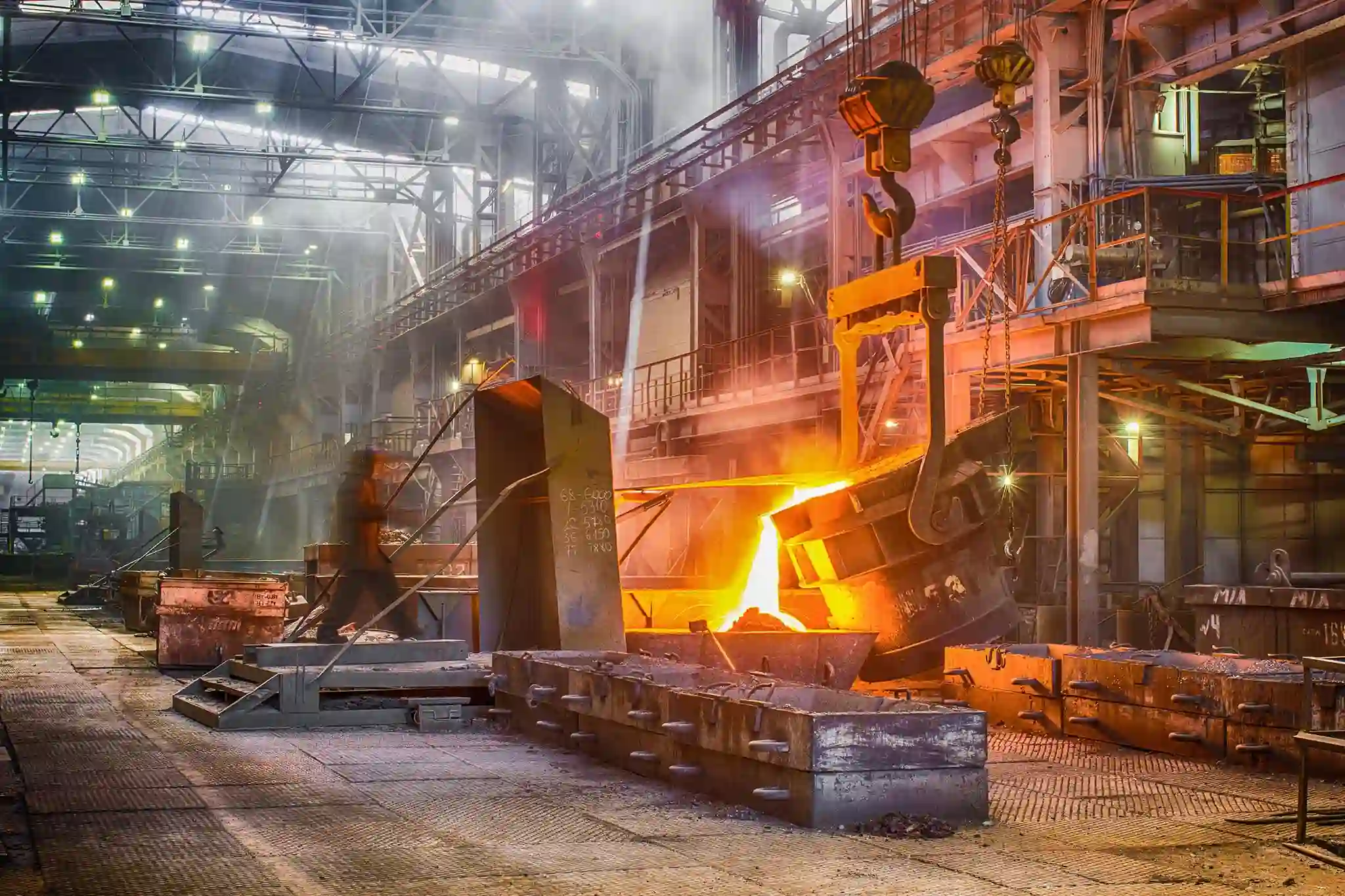
Silicon carbide, also known as emery, is rarely natural and mostly used in industry as synthetic raw materials. It has two crystal forms: β-SiC in the low-temperature form, which has a cubic structure, and α-SiC in the high-temperature form, which has a hexagonal structure. Its true density is 3.21g/cm3, and its decomposition (sublimation) temperature is 2600°C. It is a hard material with a Mohs hardness of 9.2. The thermal expansion coefficient of SiC is not large. In the range of 25℃~1400℃, the average thermal expansion coefficient of SiC is 4.4×10-6/℃.
Silicon carbide has a high thermal conductivity (58.6W/m·K). Due to the different measurement methods, porosity and pore shapes of the tested samples, the values in the literature are not completely consistent. Generally, the higher the SiC content, the lower the temperature, and the greater the thermal conductivity. Low thermal expansion coefficient and high thermal conductivity can make SiC refractory materials have good thermal shock stability.
At low temperatures, silicon carbide has relatively stable chemical properties and excellent corrosion resistance, and is not corroded by boiling hydrochloric acid, sulfuric acid and hydrofluoric acid. However, it can react with certain metals, salts, and gases at high temperatures. Silicon carbide is stable up to 2600°C in a reducing atmosphere, but oxidation will occur in a high-temperature oxidizing atmosphere: SiC+2O2→SiO2+CO2 (1)
Application of silicon carbide in refractory materials
Silicon carbide is widely used as a high-performance refractory material or as a method to improve the performance of refractory materials, especially the resistance to Additives for slag resistance and thermal shock stability are used.
Application of silicon carbide in shaped refractory materials:In shaped refractory materials, SiC can be used as the main component to make SiC products, or as an additive component to make semi-silicon carbide products.
Silicon carbide refractory material refers to an advanced refractory material with silicon carbide as the main component, which is fired from industrial silicon carbide as raw material. It is also called silicon carbide product. Silicon carbide products can be classified according to silicon carbide content, type and amount of binder. The performance of the material depends to a large extent on the bonding status between silicon carbide particles in the material, so it is usually classified by bonding. Phase types classify silicon carbide products. According to the different bonding phases, silicon carbide products can be divided into: oxide bonded silicon carbide, nitride bonded silicon carbide, self-bonded silicon carbide , siliconized reaction sintered silicon carbide wait
Semi-silicon carbide (SiC)-based products are silicon carbide (SiC)-containing refractory products with silicon carbide (SiC) as a secondary component or auxiliary component. According to its different materials, it can be divided into clay clinker silicon carbide (SiC) products, high alumina silicon carbide (SiC) products and corundum silicon carbide (SiC) products. Because these products contain silicon carbide (SiC), their thermal shock stability, thermal conductivity and strength are significantly improved. For example, adding a small amount of silicon carbide (SiC) to clay clinker silicon carbide (SiC) products has a significant effect on improving the thermal shock stability of the product. As the silicon carbide (SiC) fine powder content in the ingredients increases, the thermal shock stability of the product increases. The shock stability is gradually improved; by adding an appropriate amount of silicon carbide (SiC) (the most suitable amount is 30%) and adding an appropriate amount of phosphoric acid to high-aluminum silicon carbide (SiC) products, the products have high thermal shock stability and good thermal conductivity. , its strength is also high; adding a small amount of silicon carbide (SiC) fine powder to corundum silicon carbide (SiC) products can significantly improve its thermal shock stability. As the amount of silicon carbide (SiC) fine powder increases, the thermal shock stability Regularly improve, such as using brown corundum as aggregate, adding 10% silicon carbide (SiC) fine powder, using phosphoric acid as a binding agent, high-pressure molding, and heat treatment at 1450°C to produce slide rail bricks for rolling heating furnaces. The application works well.