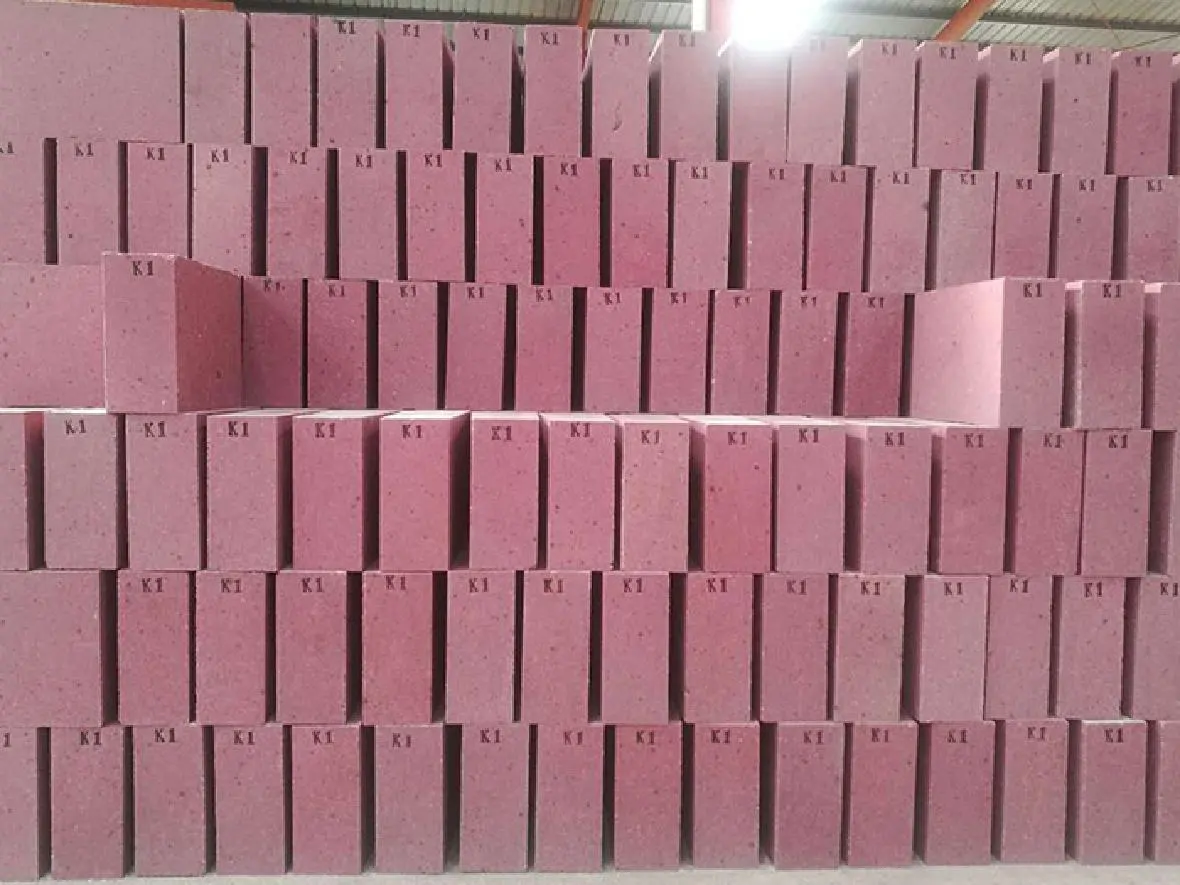
Corundum bricks are refractory bricks with alumina as the main raw material. All refractory bricks with a content of more than 90% can be called corundum bricks, but corundum bricks also have different contents. Pure corundum and high-alumina bricks are refractory bricks with a certain proportion of corundum added; chrome corundum bricks are refractory bricks with different proportions of Cr2O3 added to raw materials with high aluminum content. Their raw material components are different.
However, the production of these two bricks is basically the same, and both are formed by high pressure and sintered at high temperature. However, the sintering temperature is slightly different, and the temperature of chrome corundum bricks is about 20℃ higher. However, if the chrome corundum bricks used at the bottom of the glass kiln are cast, the price is several times higher than that of sintered corundum bricks. Even if the two bricks are sintered in the same way, the price of chrome corundum bricks is relatively higher than that of corundum bricks.
The operating temperature of corundum bricks is about 1600℃; the operating temperature of chrome corundum bricks is about 1700℃, and the load softening temperature is also different, corundum bricks are at 1600, chrome corundum bricks ≥1700℃, and the operating temperature of chrome corundum bricks is better than that of corundum bricks.
The maximum compressive strength of corundum bricks is about 100MPa, and the room temperature compressive strength of chrome corundum is about 120MPa. The compressive strength of chrome corundum bricks is also significantly higher than that of corundum bricks.
The thermal shock stability of chrome corundum bricks will decrease with the increase of Cr2O3 content. Chrome corundum bricks with lower Cr2O3 content have better thermal shock stability than bricks with higher Cr2O3 content. Generally speaking, the Cr2O3 content of chrome corundum bricks is between 12% and 20%; especially for AKZ type chrome corundum bricks, the thermal shock stability will be improved by adding a small amount of additives that produce phase change. However, the thermal shock stability of corundum bricks is not as good as that of chrome corundum bricks. To adjust the thermal shock stability, a certain proportion of silicon carbide should be added.
The slag erosion resistance of corundum refractory bricks is not as good as that of chrome corundum bricks. When corundum bricks are severely eroded by slag, the slag will penetrate into the bricks and penetrate to the surface along the pores inside the bricks; chrome corundum bricks are almost not eroded by slag, and there is a clear boundary between the edge of the inner hole and the residue, which rarely penetrates into the bricks. However, under low temperature conditions, the slag resistance of corundum bricks is also acceptable. This depends on the type of furnace and the lining used, which is determined by the temperature and the degree of erosion.
In addition, the use of chrome corundum bricks is different: chrome corundum bricks are used for glass kiln bottoms, garbage incinerators, gasification furnace linings, etc. Corundum bricks are used in cracking and conversion furnaces in the petrochemical and fertilizer industries, and steelmaking furnaces and blast furnaces in the metallurgical industry. Corundum bricks are cheaper than chrome corundum bricks. When the temperature is suitable, it is also a reasonable choice to choose corundum bricks to reduce production costs.
The difference between corundum bricks and chrome corundum bricks makes them play different roles under different environments and process requirements. Choosing the right material can improve the service life and effect of the equipment and reduce costs. Therefore, when choosing which brick to use, the characteristics and differences of corundum bricks and chrome corundum bricks should be considered to meet the needs of furnace lining.