Among the stably operating power systems around us, those fast-moving electric cars, and even those spacecraft traveling in space, there is a mysterious material that is quietly playing a huge role, and that is silicon carbide (SiC). This material that is resistant to high temperatures, withstands high voltages, and has amazing thermal conductivity makes it a revolutionary material choice in many fields such as semiconductors, aerospace, and power electronics. In other words, many modern technologies simply would not be possible without silicon carbideBut preparing silicon carbide is not as easy as simply mixing two elements. There are high temperatures, high pressures, and complex processes that are accurate to the micron level. Every step requires precise calculation, and every detail cannot be sloppy. Today we will talk about this mysterious and powerful material, and see what technical difficulties there are in preparing silicon carbide, and how to overcome these difficulties step by step.
So, what is so great about silicon carbide? Its chemical and physical properties are like superhero powers, making it the best in the materials world. First, speaking of hardness, silicon carbide is as hard as diamond, which makes it excellent as an abrasive and cutting tool. Its thermal conductivity is also first-class, which has great potential in the application of heat dissipation materials. Looking at its chemical properties, silicon carbide is indifferent to almost all acids and alkalis. This chemical stability allows it to operate calmly in extreme environments. As for heat resistance, the pots and pans we usually use have to be careful when encountering high temperatures, but what about silicon carbide? It can maintain its structure unchanged at temperatures up to thousands of degrees, which is very important in the heat-proof materials of spacecraft. has natural advantages.
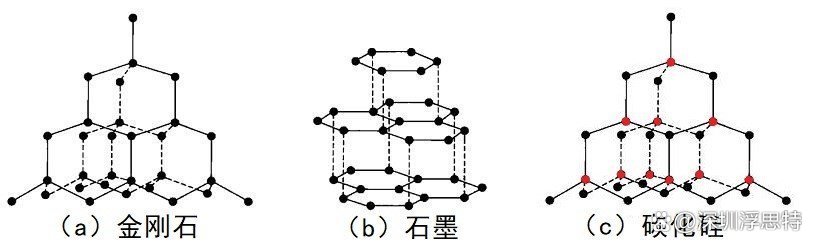
Let's talk about its crystal structure. Silicon carbide is not static. It has several crystal forms, such as cubic silicon carbide (3C-SiC), hexagonal silicon carbide (6H-SiC) and the most common tetragonal silicon carbide ( 4H-SiC). These different crystal structures allow silicon carbide to show its talents in different application scenarios. Simply put, silicon carbide is an all-rounder. No matter which field it is in, it can bring us unexpected performance.
In fact, preparing silicon carbide is like cooking a complicated dish, with various methods, each with its own uniqueness. The traditional method is Acheson craft, which is a craft left by our ancestors and is still used today. It is to mix silica sand and carbon powder in proportion, then burn it over a high fire, the temperature can reach more than 2,000 degrees Celsius, and then the silicon and carbon are transformed into the silicon carbide we want. Although this method has a long history, to be honest, it pollutes the environment, consumes high energy, and is not very efficient. Now it is increasingly unsuitable for our requirements for high performance and green environmental protection.
Here we have to mention chemical vapor deposition (CVD) technology, which is a very popular method to prepare high-quality silicon carbide. It operates just like spray painting with a spray gun, sending gases containing silicon and carbon to the surface of the substrate at high temperatures, where it is slowly deposited into a film. This method can not only produce high-purity silicon carbide, but also has good controllability and uniform thickness. However, the equipment and operation requirements are high, and the cost naturally goes up.
In addition to CVD, there are also physical methods such as laser synthesis and electron beam evaporation. When it comes to laser synthesis, it uses a powerful laser beam to decompose the raw material gas of silicon carbide, and then condenses it to form a film on a cooled substrate. It has high precision and flexible operation. As for electron beam evaporation, it bombards solid silicon carbide with electron beams, evaporates it, and then deposits it on a specific substrate. This method is suitable for producing thin film materials.
Although we have so many sophisticated preparation methods, we still have to overcome several technical difficulties to truly make silicon carbide beautiful.
First of all, high-temperature synthesis conditions are no small challenge. Silicon carbide can be formed at temperatures of 2,000 degrees Celsius or higher. This means that you have to have equipment and materials that can withstand such high temperatures. However, the real difficulty is controlling the growth rate of silicon carbide crystals. If the growth is too fast, impurities are easily doped into the crystal; if the growth is too slow, it is uneconomical. Therefore, find the perfect rate to ensure crystal quality and high efficiency at the same time.
Let's talk about raw gas. High-purity, high-stability raw gas is the key to preparing high-quality silicon carbide. However, the preparation of these gases is difficult and costly. Think about it, to make the gas pure and free of impurities, and to ensure that it is stable throughout the entire process, how meticulous must this process be!
Preparing large-area single crystal silicon carbide is even more challenging. Imagine that you have to make thousands of silicon carbide molecules sit in a neat row without any defects. This is fine for making small samples in the laboratory, but it would be very difficult to put it into industrial production. It's like trying to plant a perfect lawn on a football field, free of weeds, pests and diseases.
Finally, impurity control and doping uniformity are also technical difficulties. As you know, the properties of semiconductors depend greatly on the type and distribution of impurities and doping. If it is mixed unevenly, like a fruit salad with only apples but no oranges, the taste will definitely be wrong. The same is true for silicon carbide. If you want to have excellent performance, you must ensure the uniformity of doping.
So, how do we overcome these technical difficulties?
There are now many improvements in high-temperature synthesis technology. For example, the use of more advanced furnace materials can withstand higher temperatures without deformation, which makes temperature control more precise. Moreover, we now have more sophisticated temperature control systems that use advanced sensors and control algorithms to accurately regulate temperature during the entire crystal growth process to ensure the stability of the crystal growth rate.
For the preparation of high-purity raw gases, we now use some new methods, such as molecular sieve adsorption technology, low-temperature plasma plasma purification technology, etc. These methods not only provide higher purity feed gases, but also have the potential to be applied to large-scale industrial production.
As for the industrial-scale production potential of preparation technologies, we are seeing a shift from laboratory to industrial manufacturing. For example, silicon carbide films can be continuously produced on larger area substrates using the continuous chemical vapor deposition (CVD) method, a technology that is well suited for mass production.
Of course, impurity control and doping technology have also made great progress. Using ion implantation technology and atomic layer deposition (ALD) technology, the distribution of impurities and dopants can be controlled at the atomic level, which not only improves material performance, but also greatly increases device reliability.
In short, every step forward in silicon carbide preparation technology is a solid step for us to climb to the top. As these technologies continue to mature and innovate, we have reason to believe that silicon carbide will shine in the field of power electronics in the future, bringing us more efficient and environmentally friendly energy use.
In the technical field of silicon carbide preparation, the future development path opens up unlimited possibilities and potential. Let's take a look at these exciting future directions.
The exploration of emerging preparation technologies is bringing revolutionary changes to traditional preparation methods. For example, silicon carbide preparation based on 3D printing technology is a very potential development direction. 3D printing technology can precisely control the accumulation and structure of materials at the microscopic level, which is an ideal solution for silicon carbide products with complex shapes or special performance requirements.
What followed was the development of large-size crystal growth technology for silicon carbide. As the demand for high-power and high-efficiency electronic devices continues to grow, the demand for large-sized and high-quality silicon carbide crystals is also increasing. Future research will focus on improving the uniformity and scale of crystal growth to meet the requirements of industrial mass production.
In summary, the future development of silicon carbide preparation technology will be multi-dimensional and multi-directional. The continuous emergence of new technologies will not only promote the improvement of the performance of silicon carbide materials themselves, but also bring unprecedented opportunities to power electronics and other related fields. Let us wait and see how these technologies will light up a more energy-saving, efficient, and green future.