What is Silicon Carbide?
Silicon carbide is a chemical compound composed of silicon and carbon. It is known for its remarkable hardness, thermal conductivity, and resistance to wear and oxidation. These characteristics make it a popular choice in abrasives, refractories, and high-performance electronics. However, depending on the production method and the materials used, silicon carbide can exist in various forms, the most common of which are black and green silicon carbide.
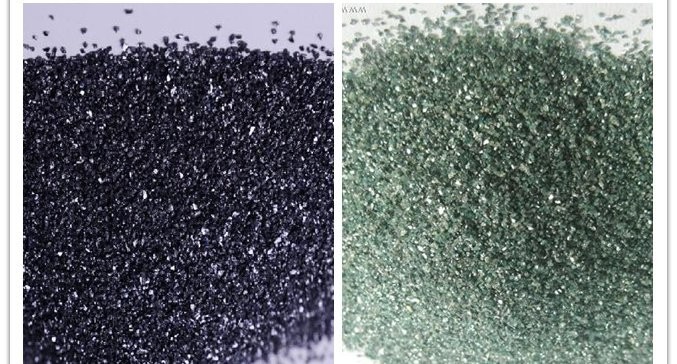
Black Silicon Carbide: Characteristics and Applications
Black silicon carbide (BSC) is produced by heating high-purity silica and carbon in an electric furnace at temperatures exceeding 2,000°C. The result is a material that exhibits unique properties suited for specific applications:
- Composition: Black silicon carbide typically contains a higher percentage of iron and other impurities, which gives it a darker color.
- Hardness: With a hardness of around 9.0 on the Mohs scale, black silicon carbide is still very hard, though slightly less so than its green counterpart.
- Applications: Black silicon carbide is widely used in applications that require strong abrasive properties, such as in grinding, cutting, and polishing. It is also used in the production of refractory materials, abrasives for metalworking, and in certain cutting tools.
- Cost-Effectiveness: Black silicon carbide is often more affordable than green silicon carbide, making it a popular choice for general-purpose applications.
Green Silicon Carbide: Characteristics and Applications
Green silicon carbide (GSC) is produced using a similar process but with higher purity raw materials and a slightly different production method. The result is a more refined and high-performance material that has distinct advantages in certain applications:
- Composition: Green silicon carbide is produced using petroleum coke and silica at high temperatures. This process results in a material that is purer, with fewer impurities compared to black silicon carbide, giving it its characteristic green color.
- Hardness: Green silicon carbide has a hardness of around 9.5 on the Mohs scale, making it slightly harder than black silicon carbide. This increased hardness makes it more suitable for precision applications.
- Applications: Green silicon carbide is particularly effective for high-precision cutting and grinding of materials such as glass, ceramics, and semiconductor wafers. It is also used in the manufacture of high-performance abrasives, such as those for polishing hard materials and in water jet cutting applications.
- Higher Cost: Due to its higher purity and specialized applications, green silicon carbide is typically more expensive than black silicon carbide.
Key Differences Between Black and Green Silicon Carbide
While both types of silicon carbide offer impressive mechanical properties, they differ in several important areas:
- Hardness: Green silicon carbide is slightly harder than black silicon carbide. This makes GSC the preferred choice for applications that require extreme precision and cutting efficiency.
- Purity: Green silicon carbide is produced using purer raw materials, which gives it a higher degree of refinement. Black silicon carbide, on the other hand, may contain more impurities, affecting its performance in certain high-precision tasks.
- Cost: Due to its higher quality and more complex manufacturing process, green silicon carbide tends to be more expensive than black silicon carbide, making BSC a more cost-effective option for general abrasive uses.
- Applications: Black silicon carbide is ideal for general abrasive applications, while green silicon carbide is more suited to high-precision tasks and industries that require superior performance, such as electronics and ceramics.
Choosing the Right Type of Silicon Carbide
Choosing between black and green silicon carbide depends on the specific requirements of your application. Consider the following factors:
- Application Type: If you need a material for heavy-duty grinding or cutting, black silicon carbide may be sufficient. For tasks requiring finer precision or a higher level of performance, green silicon carbide is the better choice.
- Cost Constraints: If cost is a major factor, black silicon carbide may offer the best balance of performance and affordability. However, for high-end applications where precision is key, the additional cost of green silicon carbide is justifiable.
- Material Hardness: For applications that involve softer materials, black silicon carbide can deliver satisfactory results. If the material to be worked on is harder or requires finer finishes, green silicon carbide will be more effective.