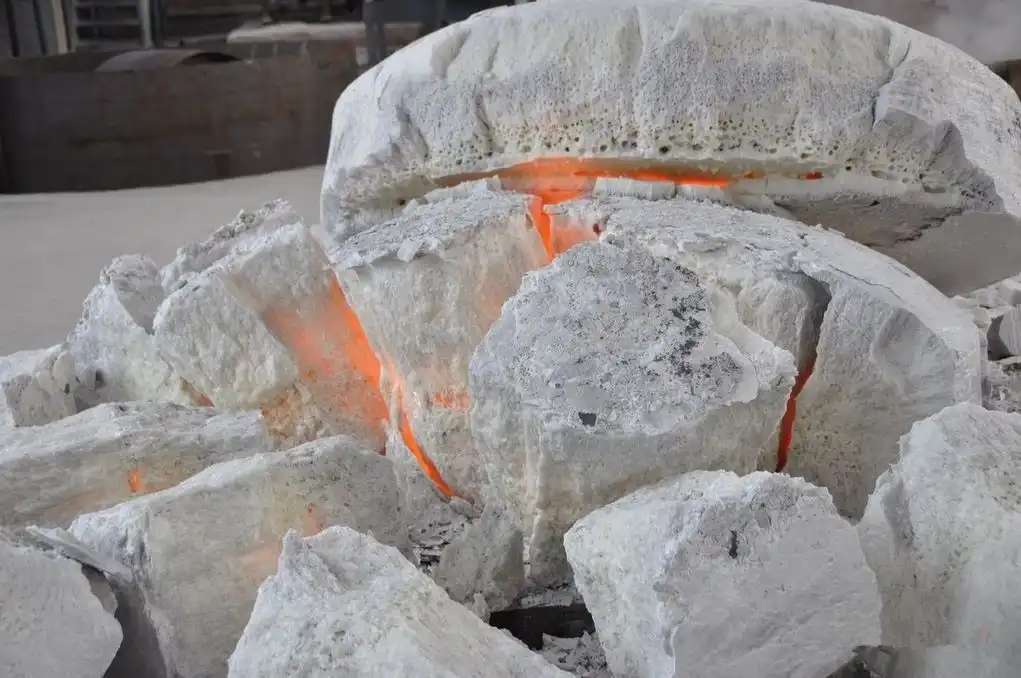
White corundum, also known as white aluminum oxide, is a versatile and highly valued material with a wide range of applications. Its exceptional hardness, purity, and abrasive properties make it a sought-after material in industries such as manufacturing, surface finishing, and refractories. In this comprehensive article, we will explore the various uses of white corundum, highlighting its key properties and benefits. By understanding the applications of white corundum, we can appreciate its significance and contribution to modern industries.
-
Understanding White Corundum
White Aluminum Oxide(WFA), also known as white Fused Alumina, is a chemical compound of aluminum and oxygen. The most common form of crystalline aluminum oxide is known as corundum. It is electrically fused in an arc furnace at 2050℃ with high purity Alum. Physical and Chemical Properties White corundum is mainly composed of aluminum oxide, which has a high melting point and excellent heat resistance. It has a Mohs hardness of 9, making it quite hard. Its chemical properties are also stable, making it a reliable material. -
Applications of White Corundum
-
1.Abrasives and Grinding
White corundum is widely used as an abrasive material in various applications, including grinding wheels, sandpapers, and abrasive powders. Its exceptional hardness, combined with its toughness, allows it to efficiently remove material, shape surfaces, and provide smooth finishes. In the metalworking, automotive, and precision machining industries, white corundum is employed for grinding, honing, and polishing applications. It effectively grinds down metal, smoothes rough surfaces, and prepares them for further treatment or coating. -
2.Refractories and Ceramics
White corundum plays a critical role in the production of refractory materials and ceramics. Its high melting point, excellent thermal stability, and resistance to thermal shock make it an ideal choice for lining furnaces, kilns, and high-temperature reactors. The refractory industry relies on white corundum to create linings that withstand extreme temperatures and harsh environments. Additionally, white corundum is used in the manufacturing of ceramic products such as crucibles, thermocouple protection tubes, and electrical insulators, where its properties ensure the durability and performance of these components. -
3.Surface Preparation and Finishing
In surface preparation applications, such as sandblasting and shot blasting, white corundum is a preferred abrasive material. Its abrasive nature allows it to effectively remove rust, scale, and paint from surfaces, preparing them for painting, coating, or further treatment. Industries ranging from metal fabrication to shipbuilding utilize white corundum for surface preparation before applying protective coatings or achieving desired surface textures. The consistent and controlled abrasiveness of white corundum ensures efficient and precise surface preparation. -
4.Precision Polishing and Lapping
White corundum's high hardness and fine particle size make it an essential component in precision polishing and lapping processes. Industries such as optics, electronics, and semiconductor manufacturing utilize white corundum for achieving high-quality finishes on optical lenses, semiconductor wafers, and other precision components. White corundum-based slurries and pastes are applied during these processes to achieve precise flatness, smoothness, and mirror-like surfaces, meeting the stringent requirements of these industries. -
5.Investment Casting
White corundum plays a crucial role in investment casting, a process used to create intricate and high-quality metal parts. In investment casting, white corundum is used as the primary material for manufacturing ceramic molds or shells. The high temperature resistance and dimensional stability of white corundum enable the production of complex metal components with fine details and intricate shapes. The ceramic molds made from white corundum maintain their shape and integrity during the casting process, resulting in precise and high-quality castings. -
6.Coatings and Surface Treatments
White corundum is incorporated into coatings and surface treatments to enhance wear resistance, hardness, and chemical resistance. It is particularly used in thermal spray coatings, where a layer of white corundum particles is deposited onto a surface to improve its properties. The resulting coating provides protection against abrasion, erosion, and chemical attack. Industries such as aerospace, automotive, and manufacturing utilize white corundum coatings to extend the lifespan of components exposed to harsh operating conditions, ensuring their durability and performance.
-
-
Benefits of White Corundum
-
1.Exceptional Hardness and Abrasive Properties
White corundum's outstanding hardness and abrasive characteristics enable efficient material removal and surface finishing, resulting in precise, smooth, and high-quality surfaces. -
2.Thermal Stability and Chemical Inertness
The thermal stability and chemical inertness of white corundum make it suitable for high-temperature applications, refractories, and environments requiring resistance to corrosive substances. -
3.Purity and Consistency
White corundum is known for its high purity and consistent composition, ensuring reliable performance and consistent results in various applications. -
4.Versatility
The broad range of applications for white corundum underscores its versatility and adaptability to diverse industries and processes, making it a valuable material choice.
-
-
Conclusion
White corundum has high hardness, purity, and grinding performance, so it has a wide range of applications in industries such as manufacturing, surface treatment, and refractory materials. Its uses include abrasives and grinding, refractory materials, ceramics, and investment casting, among other industrial applications. With the continuous development of industries and the demand for high-performance materials, the application prospects of white corundum are still very promising.